Attachments
Download our document to see specific data of the service and how we work.
For more information about SiOx coatings and how you can best use them, contact us!

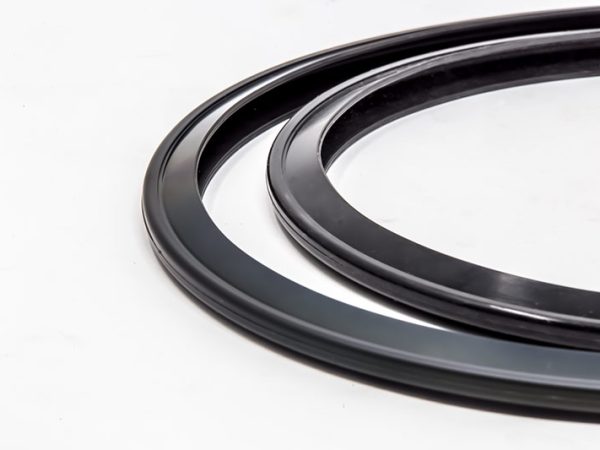

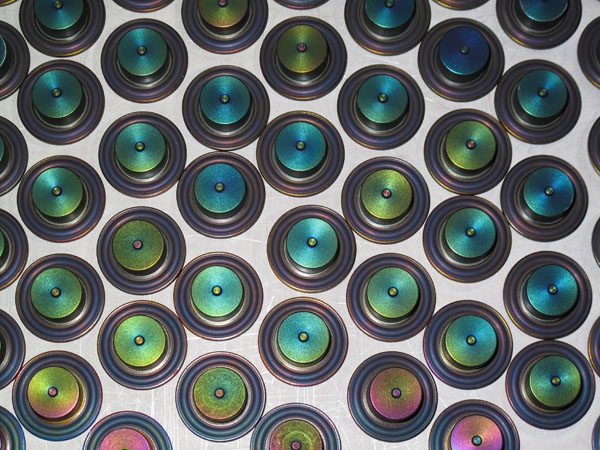
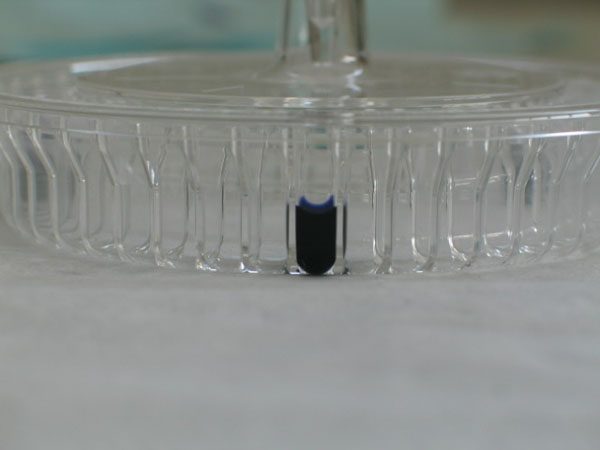
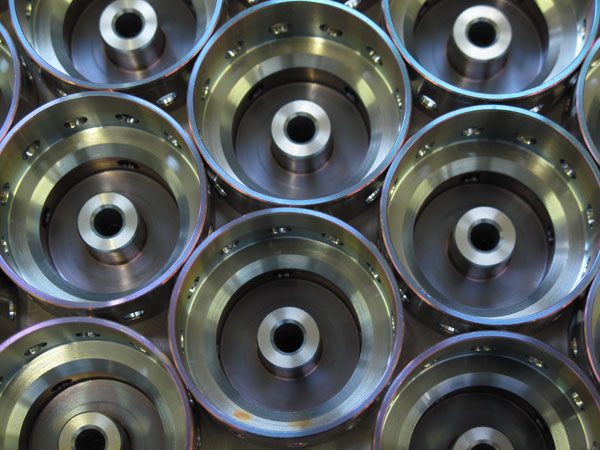
Amorphous silicon oxide is a material that can be produced in different ways, one of which is vacuum deposition.
In simple terms, silicon oxide is commonly applied as a thin, colourless film, just a few microns thick, through a process called PACVD or PECVD (Plasma-Assisted Chemical Vapor Deposition or Plasma-Enhanced Chemical Vapor Deposition)
Silicon oxide SiOx films, obtained through PECVD technology, are widely used in various industries due to their exceptional chemical and physical properties, particularly in terms of corrosion and abrasion resistance.
SiOx Coating Characteristics
The PECVD-applied amorphous silicon oxide (a:SiOx) coating is transparent or semi-transparent and possesses glass-like properties, including:
- High abrasion and scratch resistance (~800 Hv hardness).
- Excellent corrosion and oxidation resistance, thanks to chemical stability and homogeneity.
- Superior thermal stability.
- Completely dielectric (insulating) properties.
PECVD SiOx Coating Process
The deposition process occurs in a vacuum chamber under controlled atmospheric conditions, where reactive gases are ionized (plasma state) via an electromagnetic field.
Using medium- or high-frequency generators, the plasma energy ionizes the gases, leading to the formation of the SiOx film.
- Conductive materials (e.g., metals) can be connected to power source.
- Non-conductive materials (e.g., polymers) can be simply exposed to plasma generated by dedicated antennas.
The current passing between anode and cathode ionizes the gases, creating a reactive plasma.
The ions and radicals in the plasma then bombard the surface, forming the desired film.
The shape and geometry of the plasma source antennas allow for precise, uniform deposition, even on complex geometries.
By adjusting the geometry of the antennas, it is possible to concentrate the coating in specific areas or exclude others, allowing customized film distribution.
In most cases, silyl ethers are used to deliver silica into the chamber, which is then oxidized to form the SiOx film. However, monomers or solid targets can also be used via sputtering, although the first method is more efficient and cost-effective, making it the preferred industrial solution.
Key features of SiOx coating
- Exceptional uniformity.
- Superior coverage of surface irregularities.
- Increased surface hardness (mechanical protection).
- High resistance to atmospheric, chemical, and organic agents.
- Outstanding oxidation and corrosion resistance.
- Preservation of the material’s physical and chemical properties.
The silicon oxide coating enhances surface hardness, significantly improves oxidation resistance, and ensures remarkable thermal stability. Moreover, SiOx coatings are highly safe, making them suitable even for food contact or medical applications.
Compatible materials for SiOx coating
Various materials can undergo silicon oxide coating, including:
- Organic polymers
- Chromium
- Ceramics
- Titanium
- Aluminium
- Magnesium
- Light alloys
- Steel
Industrial applications of SiOx coatings
SiOx coatings are widely used across multiple industries:
- Bathroom & Kitchen Fixtures: Protection from scratches & corrosion.
- Electronics & Displays: Scratch-resistant coating for screens & observation windows.
- Toys:Abrasion & scratch protection.
- Aerospace: Corrosion resistance for satellite & aeronautical components.
- Marine Industry: Protection from salt corrosion.
- Automotive: Scratch-resistant interior protection & corrosion prevention
- Jewellery & Watches: Quartz-like appearance & elimination of nickel allergy reactions.
Variants of SiOx coating developed by ANTEC FINITURE
At Antec Finiture, we have developed various SiOx coatings, each tailored for specific applications.
By modifying the composition or adjusting the deposition method, we have optimized these coatings for different functional requirements:
- SILITEC Shield: Emphasizes mechanical protection against scratches & abrasion.
- SILITEC Seal: Enhances chemical protection & provides barrier effects for materials.
- SILITEC Wettability Plus:Increases surface wettability, reducing drying times and facilitating painting, bonding, or adhesion processes
- SILITEC Clean Plus: Optimized for easy cleaning, preventing contamination from deposits & residue buildup.